Project Background
The client is a biomass power generation enterprise with an annual output of nearly 100 million kWh. Using renewable materials such as construction waste and straw as fuel, the plant processes over 100 tons of biomass daily. Traditional manual measurement methods were not only inefficient but also posed safety risks—requiring workers to climb onto truck tops—and yielded significant inaccuracies. To address these issues, the client implemented Vi LiDAR’s truck volume measurement system to enable unattended, intelligent, and precise volumetric measurement, improving operational efficiency while cutting labor costs.
Truck volume measurement channel using LiDAR technology for accurate material volume calculation during transport.
Project Challenges
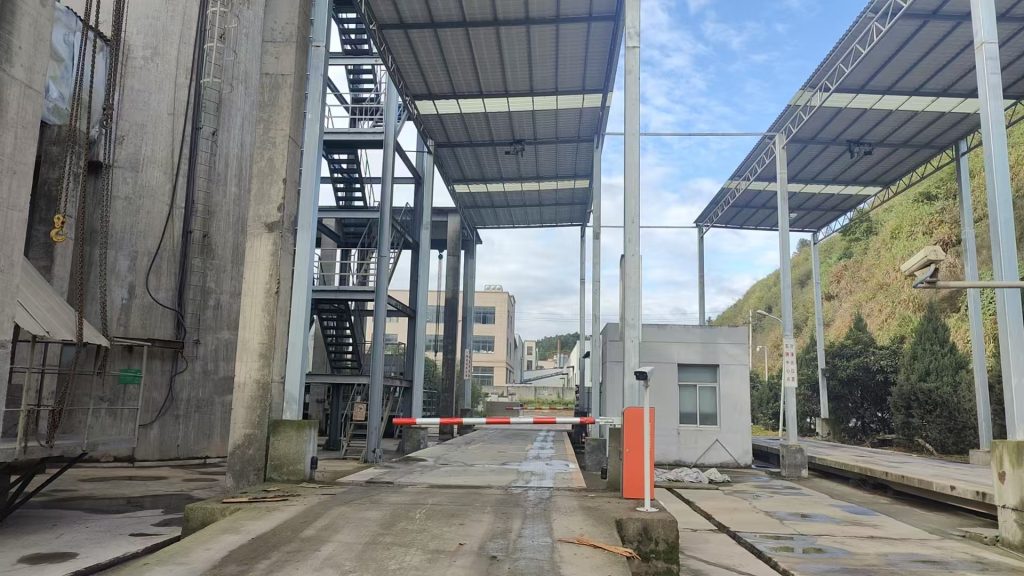
- Complex Logistics: Both inbound and outbound trucks used the same two-lane system, requiring precise recognition of whether a vehicle was entering for weighing or exiting.
- Diverse Fuel Types: Materials included construction debris, straw, bamboo offcuts, etc., each with significantly different densities—demanding highly adaptive algorithms.
- Varied Truck Sizes: Truck lengths ranged from 5m to 16m with varying compartment heights. The system needed to be universally compatible.
- High Accuracy Standards: Volume error needed to be under 3 cm, and weight conversion error below 0.5%—no room for error.
LiDAR truck volume measurement Solution Overview
Vi LiDAR volume measurement solution for precise stockpile volume calculations using advanced LiDAR technology.
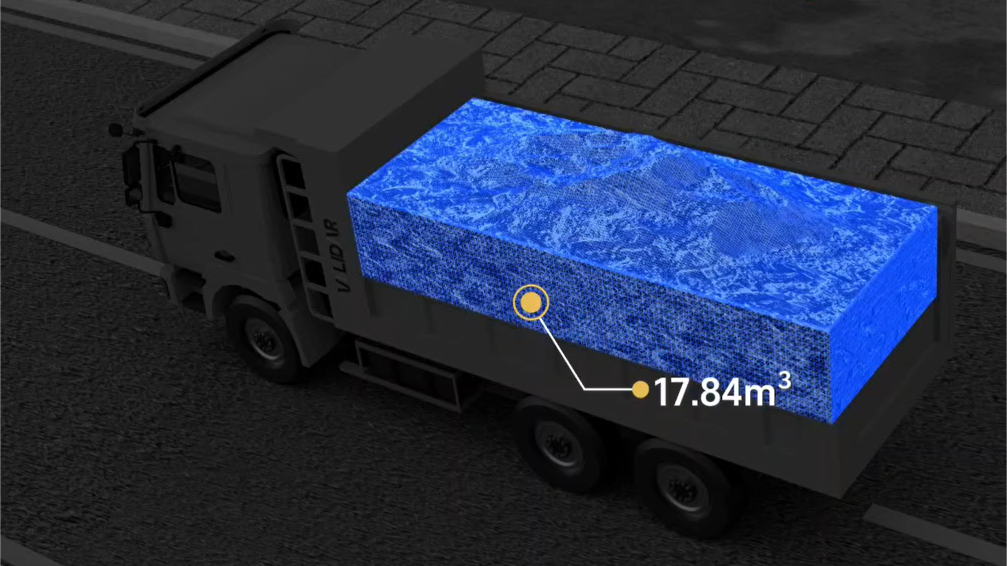
1. High-Precision Static Volume Measurement System
- Core Equipment: Equipped with a 100Hz high-speed LiDAR scanner offering 0.04° angular resolution and three times the point cloud density of conventional devices, ensuring ultra-detailed scans.
- Protective Hardware Add-ons: Dust-proof housing and a heating system were added to counteract fogging and outdoor temperature variability. With heavy dust generated during truck movement, these features ensured sensor cleanliness and measurement stability.
- Intelligent Algorithm: Automatically filters interference from dust, rain, and snow. The AI algorithm accurately detects irregularly shaped fuel piles and calculates their volume precisely.
2. Fully Unattended, One-Step Workflow
- Truck enters the scanning zone
- LiDAR completes 3D modeling in 10 seconds
- System auto-matches material type and density
- Volume + weight report generated instantly
- Data is uploaded directly to the ERP system—zero manual intervention!
LiDAR truck volume measurement system Outcomes
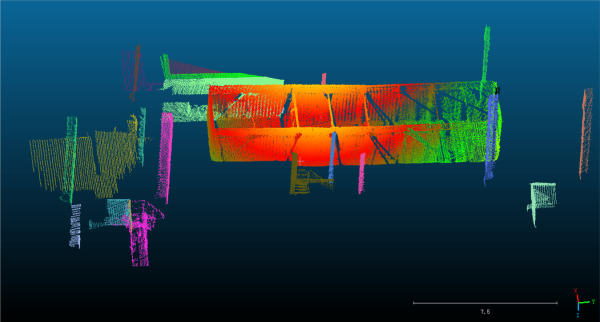
- Boosted Efficiency: Single measurement time dropped from 5 minutes to 30 seconds, increasing daily processing capacity by 10x.
- Cost Savings: Annual labor cost savings of over $150,000. Measurement disputes became a thing of the past.
- Upgraded Management: End-to-end digital process reduced fuel loss by 18%, making inventory and operations much easier to manage.
Client Testimonial
“This system not only solved our long-standing fuel measurement issues, but also helped us qualify for green finance credit—truly a win-win solution!”
— Zhang, Operations Manager, Biomass Power PlantProject Background