Project Background: Crushing Process Challenges in Cement Mining
As a leading cement producer in China with an average annual output of 4,346 tons per unit and a monthly output of 200,000 tons, the client’s mining operation follows an integrated workflow of “extraction-crushing-grinding.” However, the crushing stage posed two critical challenges:
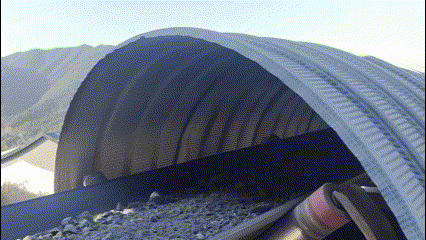
- Invisible Equipment Damage: When crusher blades wear out or fail, oversized rocks (>80mm) pass through to the grinding stage, causing clogging and shutdowns. Each unplanned downtime event can cost over ¥500,000.
- Delayed Manual Inspection: Manual rock size sampling every two hours cannot detect size anomalies in time, resulting in an average detection delay of 47 minutes.
Vi LiDAR Solution: LiDAR + AI Vision for Rock Size Intelligence
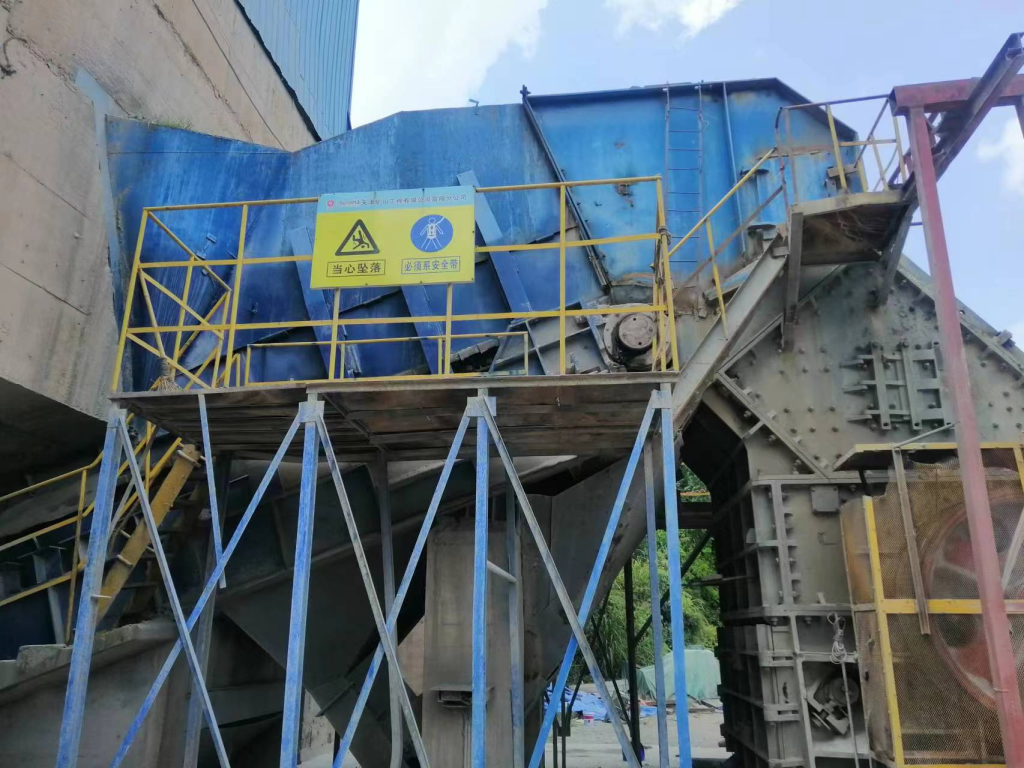
To address these issues, Vi LiDAR implemented an advanced Rock Size Distribution Monitoring System, forming a three-layer defense architecture:
1. Crusher Health Monitoring
- Millimeter-Wave LiDAR Scanning: The Vi-100 LiDAR scans the conveyor belt at 100Hz, with a precision of ±3mm.
- Blade Wear Prediction: AI analyzes fluctuations in rock size distribution. A >5% change in P80 (80th percentile particle size) triggers predictive maintenance alerts.
- Dynamic Parameter Adjustment: The system communicates with the crusher’s PLC. When oversized rocks exceed set thresholds, the crusher’s pressure is automatically adjusted.
2. Pre-Grinding Rock Screening
- 200fps Industrial Camera: The CM-200 camera captures full-width conveyor images. Foreign objects or oversize rocks are detected within 60ms.
- Multistage Rock Filtering: Rock size thresholds (e.g., <50mm) are enforced. Oversized rocks are automatically rejected using pneumatic sorters.
- 3D Point Cloud Modeling: 3D shape reconstruction ensures accurate equivalent diameter estimation, with a misclassification rate <0.8%.
3. Full-Chain Data Integration
- Edge Intelligence: The RP-8 edge box (30TOPS) processes all sensor data with <200ms latency.
- Digital Twin Visualization: Central control displays real-time heatmaps of rock size distribution, equipment health, and production forecasts.
- Predictive Maintenance: Maintenance cycles for crusher blades are suggested based on historical data, reducing breakdowns by 67%.
Real-Time Rock Size Distribution Analysis
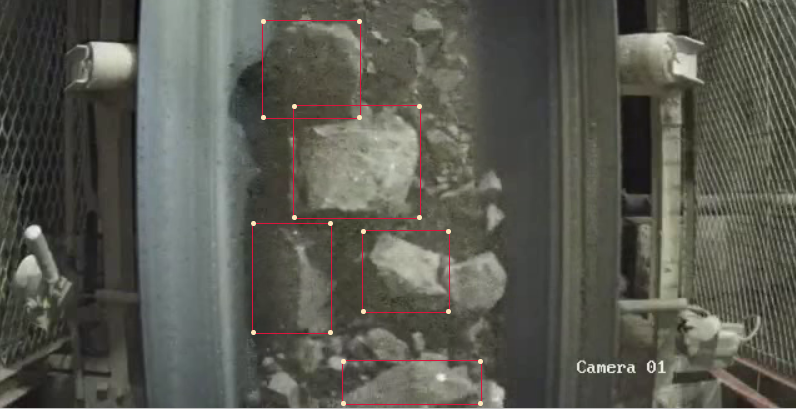
Vi LiDAR’s solution enables continuous tracking and visualization of rock size distribution across the crushing and grinding workflow. By combining LiDAR point clouds and AI visual inspection, the system automatically categorizes rock particles by size and updates distribution histograms every minute. This ensures consistent material quality and helps prevent oversized fragments from causing downstream failures.
The real-time rock size distribution dashboard provides operators with intuitive insight into material trends, improving process stability and product consistency.
Achievements: From Reactive Repairs to Predictive Control
Since implementation, the crushing process underwent a digital transformation:
- Crusher Maintenance Costs down by 30%, reducing shutdowns caused by worn blades.
- Production Efficiency improved by 25%, with consistent rock sizing and fewer bottlenecks.
- Manual Inspection Reduced by 90%, replaced by remote monitoring and alerts.
“Vi LiDAR’s system works like a CT scanner for our production line. It reveals not only the ‘inside’ of the rocks in real-time but also predicts when the equipment will need service. It has shifted our maintenance strategy from firefighting to prevention.”
— Li Zhenhua, On-Site Production Director
Core Advantages of Vi LiDAR’s Rock Size Distribution Solution
- Industrial Reliability: IP68 rating, -30°C to 70°C operation, dustproof and rugged for mining environments.
- High-Accuracy AI Models: Trained on 300,000+ rock samples, adaptable to varying geology and lighting.
- Rapid Deployment: Modular design, full installation and setup within 72 hours, compatible with major PLC/MES systems.