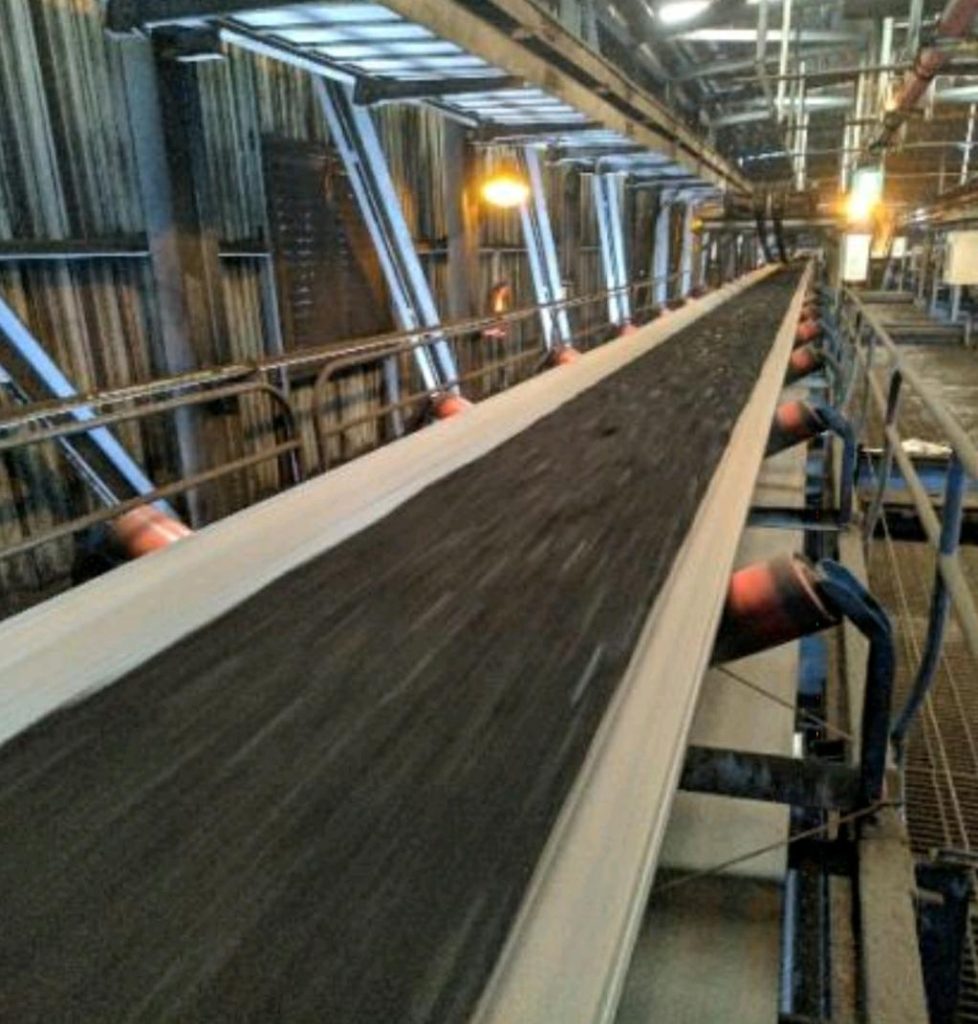
Project Background: Addressing Coal Management Challenges
PT PLN, Indonesia’s leading electricity provider, operates the PLTU Tenayan coal-fired power plant in Riau Province. The plant relies on Conveyor 04 to transport thousands of tons of coal daily to the boiler silos. Traditional manual sampling and static measurement methods presented significant challenges:
- Delayed Data: Manual measurements couldn’t provide real-time feedback on coal flow, disrupting fuel scheduling and power generation plans.
- Inaccurate Measurements: Variations in coal density led to volume-to-mass conversion errors up to 15%, affecting cost calculations.
- Safety Risks: Frequent manual inspections near operating conveyors increased the risk of workplace accidents.
To overcome these issues, PLN initiated the “LiDAR Real-Time Monitoring System” project, aiming to digitize coal transport management using 3D industrial vision technology.
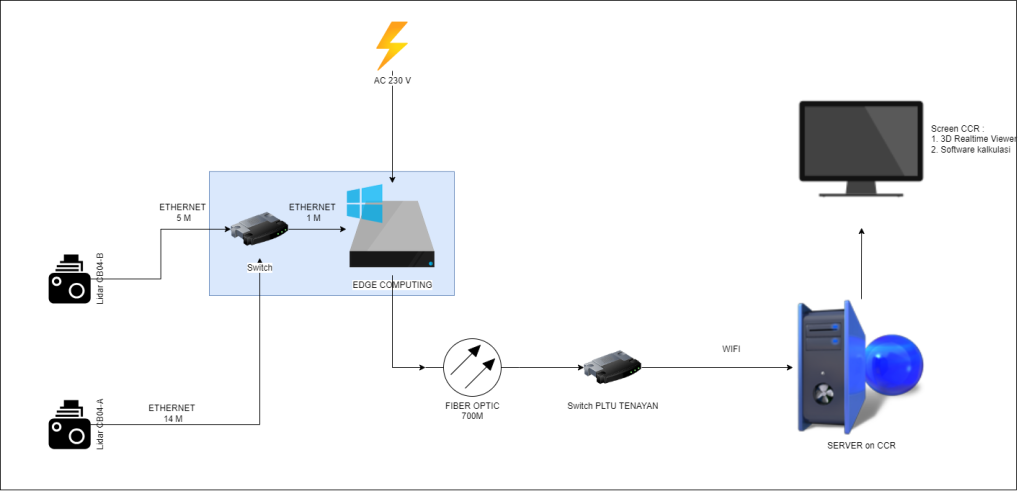
Technical Solution: ViLiDAR and Edge Computing Integration
1. Hardware Deployment: Tailored for Industrial Environments
- LiDAR Specifications:
- 270° horizontal field of view covering the full width of the conveyor.
- 40-meter detection range suitable for high-speed transport scenarios.
- IP65 protection rating and operational temperature range of -25°C to +60°C.
- 45kHz sampling rate with 0.25° angular resolution, capturing over 200,000 point cloud data per scan.
- Installation Design:
- Dual LiDAR units (04A/04B) installed at critical conveyor points (2.55 meters from the centerline, 3.65 meters high) to eliminate blind spots.
- Modular, detachable brackets for quick installation and maintenance without halting production.
2. Algorithm Engine: Converting Point Clouds into Operational Data
- Dynamic Baseline Modeling:
- LiDAR scans empty conveyor belts to create a baseline 3D model (V_empty).
- Real-time scans of loaded belts (V_lidar) are compared to the baseline to calculate coal volume (V_material = V_lidar – V_empty).
- Multi-Parameter Fusion Calculation:
- Integrates conveyor speed and historical coal density data to dynamically output mass flow (t/h), cumulative transport volume (t), and bulk density (kg/m³).
- AI algorithms automatically filter out conveyor vibrations and dust interference, achieving 98.5% accuracy.
3. System Integration: Data-Driven Decision Making
Automatic alerts for blockages or off-center loads, triggering audio-visual alarms within 2 seconds.
Edge Computing Nodes:
On-site industrial-grade servers process terabytes of point cloud data in real-time with latency under 500ms.
Supports UDP/USB protocols for seamless integration with the plant’s Distributed Control System (DCS).
Central Control Room (CCR) Visualization:
Dual-screen monitoring displaying real-time 3D coal flow models and trend analysis dashboards.
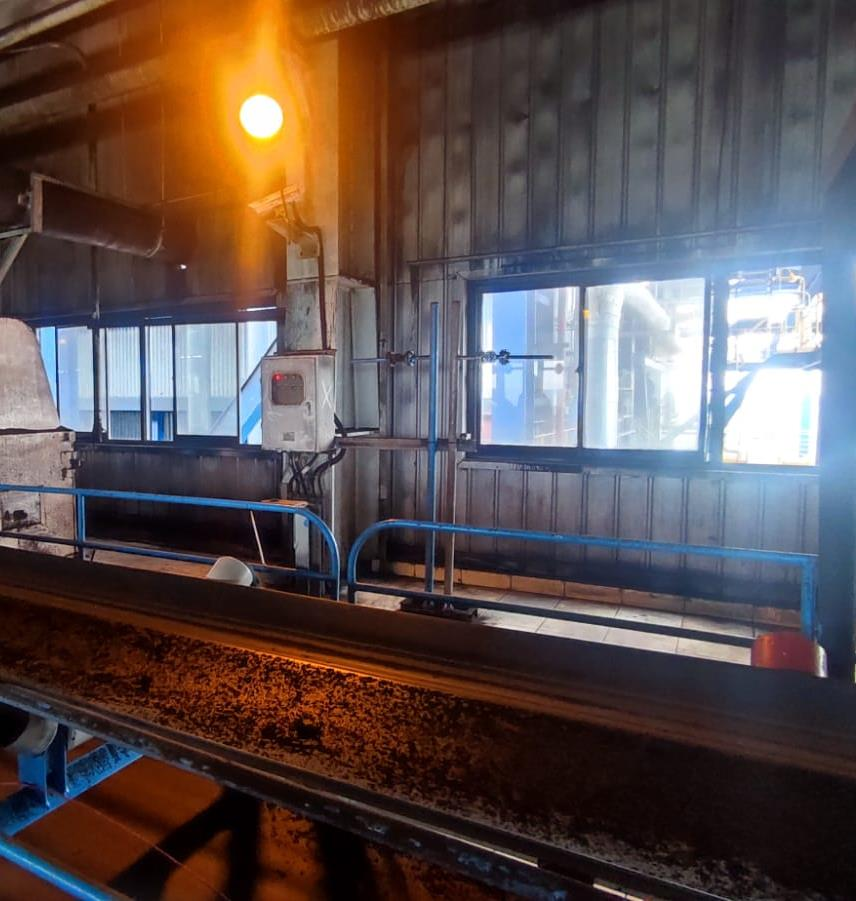
LiDAR Specifications::
- covering the full width of the conveyor.
- 40-meter detection range suitable for high-speed transport scenarios.
- IP65 protection rating and operational temperature range of -25°C to +60°C.
- 45kHz sampling rate with 0.25° angular resolution, capturing over 200,000 point cloud data per scan.
2. Algorithm Engine: Converting Point Clouds into Operational Data
- Dynamic Baseline Modeling:
- LiDAR scans empty conveyor belts to create a baseline 3D model (V_empty).
- Real-time scans of loaded belts (V_lidar) are compared to the baseline to calculate coal volume (V_material = V_lidar – V_empty).
- Multi-Parameter Fusion Calculation:
- Integrates conveyor speed and historical coal density data to dynamically output mass flow (t/h), cumulative transport volume (t), and bulk density (kg/m³).
- AI algorithms automatically filter out conveyor vibrations and dust interference, achieving 98.5% accuracy.
3. System Integration: Data-Driven Decision Making
- Edge Computing Nodes:
- On-site industrial-grade servers process terabytes of point cloud data in real-time with latency under 500ms.
- Supports UDP/USB protocols for seamless integration with the plant’s Distributed Control System (DCS).
- Central Control Room (CCR) Visualization:
- Dual-screen monitoring displaying real-time 3D coal flow models and trend analysis dashboards.
- Automatic alerts for blockages or off-center loads, triggering audio-visual alarms within 2 seconds.
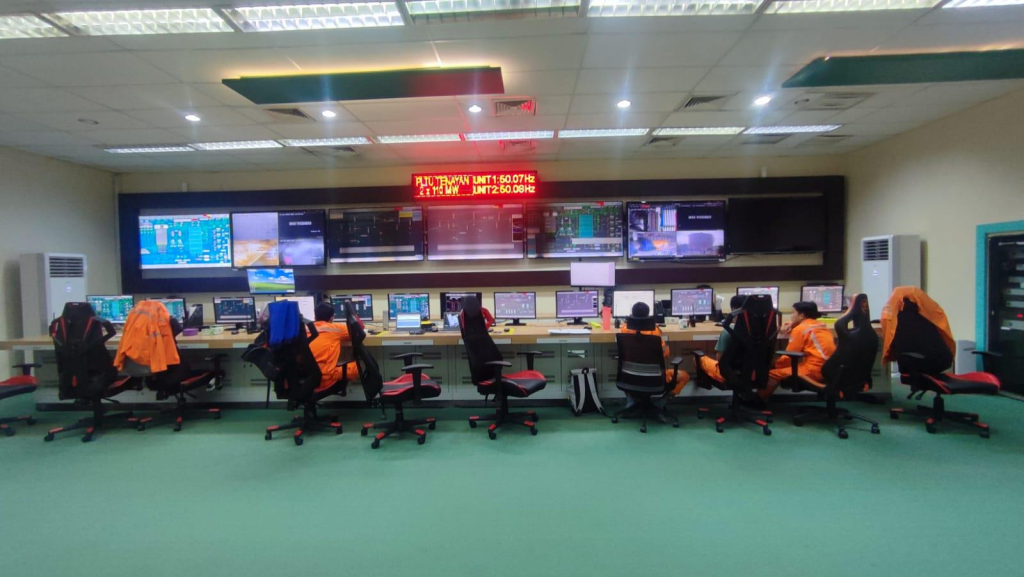
Implementation Highlights: From Design to Execution
1. Wiring Engineering: Zero Downtime Retrofit
- Fiber Optic Backbone:
- Installed 700 meters of interference-resistant single-mode fiber optics connecting edge nodes to the CCR.
- Utilized maintenance windows for installation, avoiding production interruptions.
- PoE Power Optimization:
- LiDAR and edge devices powered via Ethernet (PoE), reducing the complexity of separate power lines.
- Redundant design ensures 99.99% power supply reliability.
2. Collaborative Validation: Industry-Academia Partnership
- Three-Phase Calibration Testing with ITS:
- Laboratory calibration simulating various coal types and moisture conditions.
- 72-hour continuous monitoring of empty conveyors to confirm system stability.
- Cross-validation with weighbridge data during loaded operations, achieving error rates below 1.2%.
Results: Digital Transformation Achievements
Aspect | Traditional Method | ViLiDAR System | Improvement |
---|---|---|---|
Data Timeliness | 4–6 hours delay | Real-time updates (<1s delay) | 300% increase in decision-making efficiency |
Measurement Cost | Annual manual cost: $120,000 | Hardware maintenance: <$30,000/year | 75% reduction in operational costs |
Safety Risk | 2–3 high-risk manual inspections/month | Fully automated monitoring | Zero workplace accidents |
Client Testimonial
“Since implementing the ViLiDAR system, our fuel inventory discrepancies have decreased from 8% to 0.5%, reducing annual losses due to coal measurement errors by approximately $1.8 million. More importantly, we’ve achieved a dynamic balance between power generation planning and fuel supply for the first time.”
— PLN Tenayan Power Plant Operations Director
Conclusion
The ViLiDAR real-time monitoring system has revolutionized coal transport management at PLN Tenayan Power Plant, enhancing efficiency, accuracy, and safety. This digital transformation serves as a model for other power plants seeking to modernize their operations.